Digital transformation of injection molding industry is imperative
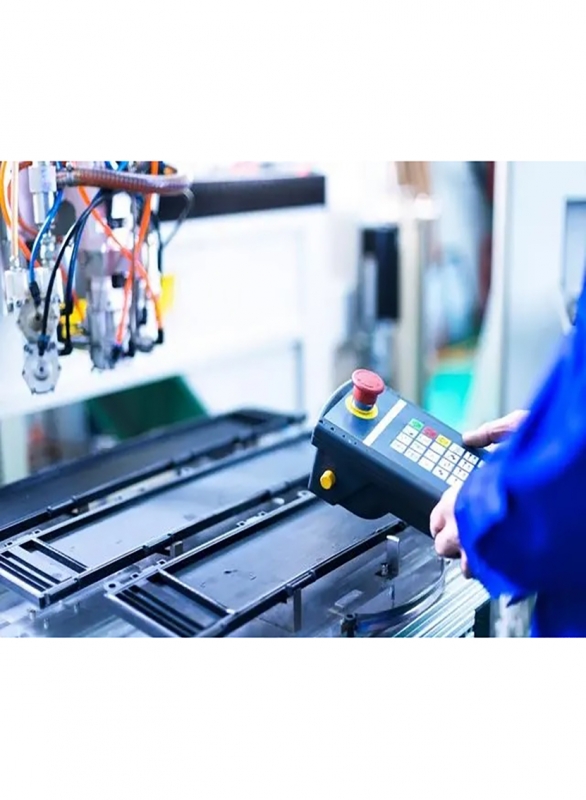
In recent years, the rapid development of the industrial Internet has given rise to emerging industries. For the traditional manufacturing industry, the impact of emerging technologies and the increasingly harsh market environment have prompted enterprises to seek further development. For the injection molding industry, digital transformation is imperative.
Digital chemical plant of injection molding industry
Industry Introduction
The huge development potential of China's injection molding industry has opened up broad space for the rapid growth of the injection molding machine industry. Almost 85% of all injection molding products must be processed through injection molding. In recent years, China's economic development has been rising in a straight line, and people's living demand is also increasing. The growing demand for injection molding products in automobile, construction, household appliances, food, medicine and other industries has promoted the development and improvement of the entire injection molding and molding technology level, and also led to the development of small and medium-sized enterprises in the injection molding industry. At present, China's injection molding enterprises have mushroomed, with considerable development potential.
Industry opportunities
In the critical period of rapid expansion of the injection molding industry, systematic and standardized management is urgently needed to reshape the internal system of the enterprise and achieve cost reduction and efficiency increase.
The injection molding industry has a large amount of data and a complex source. It is difficult to obtain complete and accurate data by manpower, resulting in the inability of enterprises to accurately calculate costs. There is an urgent need for systematic collection of production data to obtain real-time and accurate data!
Industry pain points
1. Low production efficiency
Injection molding machines and other major production equipment are not connected to the network, and production management lacks effective data support
2. Lack of standardization
There is a lack of collaborative integration between the existing injection molding production line equipment, and there is a lack of process conversion standards for product test mold to mass production, which is time-consuming and energy-consuming
3. Low automation level
The production management of injection molding enterprises depends on human resources and cannot achieve the automation of production execution and the intellectualization of production management
4. Weak management
Poor visibility of equipment, manufacturing and process quality status, lack of comprehensive analysis and unified management of real-time data, and weak management